"Delivering Clear Benefits for Everyone"
Fuel Efficiency
Automakers follow a multipronged approach in achieving fuel efficiency: from engineering lighter structures to the adoption of new powertrain technology and increased emphasis on aerodynamics. Vehicles today are multi-material utilizing more complex materials like high-strength steels, aluminium, magnesium and carbon composites. PRAZASTINAV Compositech Pvt Limited (PCPL) provides industry proven solution for structural design and optimization and helps designers and engineers to develop lightweight, structurally efficient, and innovative vehicles reducing weight and material costs while managing performance requirements.
Performance and Comfort
PRAZASTINAV Compositech Pvt Limited (PCPL)'s NVH, fluid flow and vehicle dynamics solutions drive physical prototype development by directly simulating the end customer experience dramatically improving vehicle performance and comfort. Exterior and internal fluid flow studies with PRAZASTINAV Compositech Pvt Limited (PCPL) PCPL provide insight on aerodynamics, cooling, noise, and comfort.
Safety
Safety remains an essential component in today's vehicle offerings, with pre-crash technologies (active safety) in particular gaining more focus lately. A growing number of OEMs are able to produce vehicles with good safety records. New consumer protection protocols keep challenging the status quo in term of passive safety performance pushing increasingly tougher requirements and advocating the importance of vehicle safety in all markets.
We can cater to many products which includes but not restricted to the following:
- Fenders
- Hood
- Tonneau Cover
- Headlamp Reflectors
- Oil sumps
- Valve covers
- Bumpers
- Engine Hoods and Tractor Hoods
- Motor Covers
- Dash and Instrument Covers (Soft-Touch - Urethane)
- Bumpers and Wheel Covers
- Shrouds and Cowl Assemblies
- Cab Roofs, Doors and Floors
- Exterior Roof, Side, Body and Trim Panels
- Operator Compartments and Cab Consoles
- Interior Trim
- Fuel Tanks and Fluid Reservoirs
- Body panel stiffeners
- Floorboards and firewall panels
- Carbon ducting for braking systems
- Splitters & air dams
- Engine compartment
- Water pump
- Suction area
- Clutch mounting parts
- Gear mounting parts
- Gear mounting Electric starter
- Interior Application
- Ashtray
- Wheel tubs
- Under body noise shields
- Seat frames
- Battery trays
- Load floors
- Body panels
- Under engine covers
- Reinforcement beams
- Throttle bodies and inlets
Current state of the market
To improve vehicle safety, noise and vibration, and fuel economy, automobile companies are constantly launching new materials, with most of them focusing on lightweighting. While cars of the past consisted of entirely steel-based products, manufacturers are now transitioning towards aluminum, the fastest-growing lightweight material, as well as magnesium and composite materials that deliver enhanced performance. The following figure represents the current materials being used for different automobile parts.
Vehicles today are predominantly steel structures, with some use of aluminum. The grades of steel range from mild (270 megapascal (Mpa) tensile strength) to hot-formed boron (1,500 Mpa plus tensile strength). Magnesium and polymer composites are used in some components, mostly on higher-end vehicles.
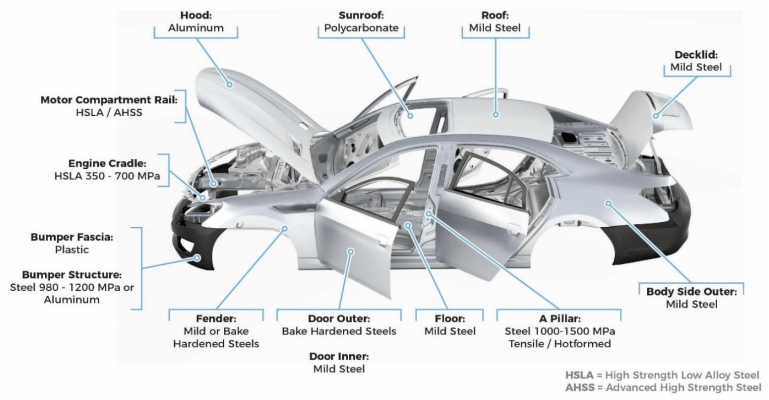
Reliable Chemistry for Composite Applications
Our wide range of automotive composite solutions answers the growing need for both high performance and mass‑production cycle times.
Battery Housing
The battery housing is a critical element of any electrified vehicle—it protects the batteries from environmental hazards, and acts as a protective barrier for passengers in case of battery malfunctions. Composite materials are lightweight, and they offer resistance to fire, crash damage and corrosion. Huntsman's composite solutions meet all safety, mechanical and thermal requirements.
Body in White
Lightweighting is critically important for electrified vehicles, as it compensates for high battery weight, reducing energy consumption and enabling longer range and/or lower battery cost. Composite materials are light, and resistant to fire, crash damage and corrosion. Huntsman offers resin systems optimized for production of composite chassis, body-in-white parts and underfloor panels.
Wheel
Composite materials are ideal for automotive wheels, as they combine light weight with high stiffness and strength. Using composite wheels reduces unsprung weight, which improves traction and control, while composites’ greater stiffness translates to a more dynamic driving experience. Huntsman offers a range of resin systems optimized for production of composite wheels.
Leaf Spring
Composites' high strength-to-weight ratio, fatigue resistance and natural frequency qualities make them an excellent choice for leaf spring applications. A composite leaf spring can be up to five times more durable than a steel spring. Huntsman's composite solutions offer industry-leading performance as we work closely with customers to optimize production processes.
Pressure Vessel
Pressure vessels, commonly used to store compressed natural gas, are increasingly in demand to store hydrogen in fuel cell vehicles. Composites' high strength-to-weight ratio makes them a good choice for hydrogen pressure vessels, which require high impact and chemical resistance, as well as high strength to withstand the high operating pressures and constant filling and emptying cycles.
Pressure Vessel
Pressure vessels, commonly used to store compressed natural gas, are increasingly in demand to store hydrogen in fuel cell vehicles. Composites' high strength-to-weight ratio makes them a good choice for hydrogen pressure vessels, which require high impact and chemical resistance, as well as high strength to withstand the high operating pressures and constant filling and emptying cycles.