Optimising Creativity and Productivity from Concept to Mass Production
Optimised Weight Design
The increase in global competition and environmental awareness has necessitated the development of optimum weight aerospace structures. Aligning our expertise of using optimization technology to determine minimum weight metallic or composite structures, we have been instrumental in pioneering the establishment of Optimization Centres at major aerospace OEMs.
Composites Design and Manufacturing
PRAZASTINAV Compositech Pvt Limited (PCPL) is at the forefront of technology and its application to take full advantage of composites in the development of light-weight, high-performance structures. Through our Composites Design Environment, aerospace clients can determine optimal ply lay-up structures for weight and performance, quickly synthesize and model concepts, and accurately predict impact damage including Fibre and matrix failure, delamination, rupture and crack propagation.
Advanced Simulation & Analysis
We have experience developing complex high fidelity finite element models to facilitate predictive virtual testing including wings, engines and aircraft interiors. In addition, we have simulated and successfully correlated against vulnerability events such as: Bird strike, Tire burst, Ditching, Passenger safety, Impact
Fiberglass and carbon fiber composites are well known. They’ve even helped revolutionize the aerospace industry. But what will the future of composites in aerospace look like?
The sky’s the limit with new composite materials set to shake up the industry. Let’s examine some of the benefits of composites, and get a glimpse of where things are going.
Aligning our expertise of using optimization technology to determine minimum weight metallic or composite structures, we have been instrumental in pioneering the establishment of Optimization Centres at major aerospace OEMs.
PRAZASTINAV Compositech Pvt Limited (PCPL) is at the forefront of technology and its application to take full advantage of composites in the development of light-weight, high-performance structures.
Through our Composites Design Environment, aerospace clients can determine optimal ply lay-up structures for weight and performance, quickly synthesize and model concepts, and accurately predict impact damage including fiber and matrix failure, delamination, rupture and crack propagation.
At PRAZASTINAV Compositech Pvt Limited (PCPL) we are therefore focusing on the serial production of composite components. We are transferring our comprehensive expertise and highly efficient materials, increasingly from the automotive sector and other industries to aerospace.
Our product portfolio already includes a wide range of prepregs and semi-finished textile fiber products for secondary structural components for aerospace, such as interior elements including floor panels, partition walls and water/wastewater systems. To speed up growth in this market segment, we also entered into a development cooperation with different types of Global leaders to bring fiber composites for primary structures, based on large-tow carbon fibers to the market for the first time.
In the small aircraft, helicopter and air taxi sector, we even offer a full range of services from engineering to finished components.
We have experience developing complex high fidelity finite element models to facilitate predictive virtual testing including wings, engines and aircraft interiors.
In addition, we have simulated and successfully correlated against vulnerability events such as: Bird strike, Tire burst, Ditching, Passenger safety, Impact.
We have experience developing complex high fidelity finite element models to facilitate predictive virtual testing including wings, engines and aircraft interiors.
In addition, we have simulated and successfully correlated against vulnerability events such as: Bird strike, Tire burst, Ditching, Passenger safety, Impact.
aircraft and spacecraft, from hot air balloon gondolas and gliders to passenger airliners, fighter planes, and the Space Shuttle. Applications range from complete airplanes such as the Beech Starship to wing assemblies, helicopter rotor blades, propellers, seats, and instrument enclosures.
The types have different mechanical properties and are used in different areas of aircraft construction. Carbon fiber, for example, has unique fatigue behavior and is brittle, as Rolls-Royce discovered in the 1960s when the innovative RB211 jet engine with carbon fiber compressor blades failed catastrophically due to bird strikes.
Whereas an aluminum wing has a known metal fatigue lifetime, carbon fiber is much less predictable (but dramatically improving every day), but boron works well (such as in the wing of the Advanced Tactical Fighter). Aramid fibers (‘Kevlar’ is a well-known proprietary brand owned by DuPont) are widely used in honeycomb sheet form to construct very stiff, very light bulkhead, fuel tanks, and floors. They are also used in leading- and trailing-edge wing components.
In an experimental program, Boeing successfully used 1,500 composite parts to replace 11,000 metal components in a helicopter. The use of composite-based components in place of metal as part of maintenance cycles is growing rapidly in commercial and leisure aviation.
Overall, carbon fiber is the most widely used composite fiber in aerospace applications.
Aerospace Aircrafts Structural parts like
- Control surfaces
- Wing parts
- Fuselage panels,
- Radome
- Interior parts,
- Fan containment cases,
- Fairings (Monolithic & Sandwich),
- Ailerons, empennage etc.
Helicopters - Structural parts like:
- Control surfaces
- Floor panels
- Cabins
- Rotary wings etc.
Space Vehicles Structural Parts:
- Composite antennae & reflectors
- Bus structures
- Towers & Sub systems
- Deployable booms & Masts
- Precision Optical structures etc.
- Compression Moulded Kevlar parts for Engines.
Advantages
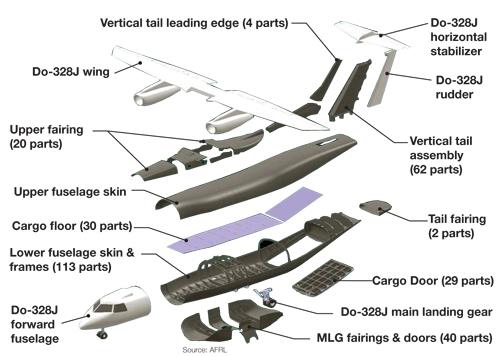
We have already touched on a few, such as weight saving, but here is a full list:
- Weight reduction - savings in the range of 20%-50% are often quoted.
- It is easy to assemble complex components using automated layup machinery and rotational molding processes.
- Monocoque ('single-shell') molded structures deliver higher strength at a much lower weight.
- Mechanical properties can be tailored by 'lay-up' design, with tapering thicknesses of reinforcing cloth and cloth orientation.
- Thermal stability of composites means they don't expand/contract excessively with a change in temperature (for example a 90°F runway to -67°F at 35,000 feet in a matter of minutes).
- High impact resistance - Kevlar (aramid) armor shields planes, too - for example, reducing accidental damage to the engine pylons which carry engine controls and fuel lines.
- High damage tolerance improves accident survivability.
- 'Galvanic' - electrical - corrosion problems which would occur when two dissimilar metals are in contact (particularly in humid marine environments) are avoided. (Here non-conductive fiberglass plays a role.)
- Combination fatigue/corrosion problems are virtually eliminated.
Future Outlook
With ever-increasing fuel costs and environmental lobbying, commercial flying is under sustained pressure to improve performance, and weight reduction is a key factor in the equation.
Beyond the day-to-day operating costs, the aircraft maintenance programs can be simplified by component count reduction and corrosion reduction. The competitive nature of the aircraft construction business ensures that any opportunity to reduce operating costs is explored and exploited wherever possible.
Competition exists in the military too, with continuous pressure to increase payload and range, flight performance characteristics, and ‘survivability’, not only of airplanes but of missiles, too.
Composite technology continues to advance, and the advent of new types such as basalt and carbon nanotube forms is certain to accelerate and extend composite usage.
So the benefits of composite materials in aerospace applications are many—but what does the future hold?
There is endless room for future growth when it comes to composites in aerospace. The demand for lighter weight materials will only increase. As aircraft fly higher and go faster, composite materials will continue to evolve.
For the time being, aircraft design includes a mixture of composites and good old-fashioned metals.
Let’s look at three ways companies are investigating the future of composites in aerospace.
We have excelled in the field of precision resin transfer molding (RTM) and conventional composites. We take an unbiased materials and processing approach when transitioning composite applications into steady production. Our experienced staff works with state-of-the-art manufacturing processes materials to develop and produce “technically challenged” composite designs.
We specialize in highly complex integrated structures and applications requiring very specific mechanical, thermal, or dimensional specifications. Our unique Liquid Resin Molding processes (RTM, VARTM etc) and our extensive knowledge in rate production put us ahead of the competition. PRAZASTINAV Compositech Pvt Limited (PCPL) is your number one choice for composite development and manufacturing.
When it comes to aerospace, composite materials are here to stay.